Big data is rapidly transforming the landscape of chemical manufacturing, bringing a new level of precision and insight to an industry that has traditionally relied on experience-based decision-making. As chemical companies navigate an increasingly complex and competitive market, the ability to harness vast amounts of data from various sources has become a critical differentiator. By leveraging big data, companies can optimize processes, improve product quality, and make more informed decisions that drive innovation and growth.
Enhance Operational Efficiency with Big Data
One of the most significant benefits of big data in chemical manufacturing is its potential to enhance operational efficiency. Chemical plants generate massive amounts of data daily from sensors, machines, and other equipment. When analyzed effectively, this data can provide deep insights into production processes, helping companies identify inefficiencies and bottlenecks that may not be immediately apparent.
For instance, by analyzing data from production lines, companies can pinpoint areas where energy consumption is higher than expected or where equipment may be underperforming. This allows for targeted improvements that can reduce waste, lower energy costs, and increase overall productivity. Additionally, big data can facilitate real-time monitoring and control of production processes, enabling more agile and responsive operations. Companies can adjust parameters on the fly, ensuring that production stays within optimal conditions and that product quality remains consistently high.
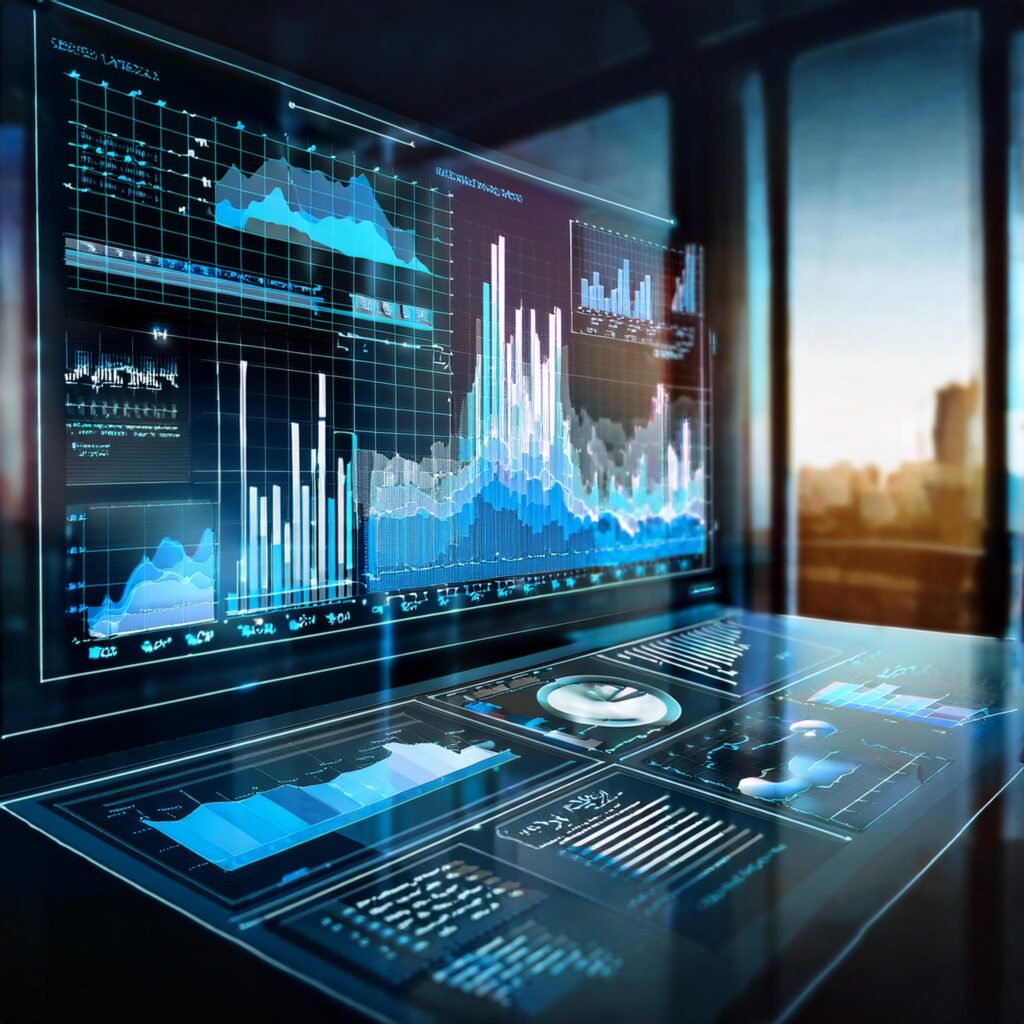
Predictive Maintenance: Reduce Downtime and Costs
Another critical application of big data in chemical manufacturing is predictive maintenance. Traditional maintenance schedules are often based on fixed intervals or reactive strategies, which can lead to unexpected equipment failures, costly repairs, and unplanned downtime. However, by analyzing historical data and real-time sensor information, companies can predict when equipment is likely to fail and perform maintenance just before it’s needed.
Predictive maintenance not only reduces the likelihood of unexpected breakdowns but also extends the lifespan of critical equipment by ensuring it is maintained in optimal conditions. This approach can significantly reduce maintenance costs and improve operational uptime, making production more reliable and cost-effective. In a competitive industry where downtime can translate to significant financial losses, the ability to predict and prevent equipment failures offers a substantial advantage.
Leverage Customer Insights and Market Trends
Beyond operational efficiency, big data also plays a crucial role in understanding customer preferences and market trends. Chemical manufacturers can analyze data from sales, customer feedback, and market research to identify emerging trends and shifts in consumer demand. This enables companies to develop products that better meet customer needs and respond more quickly to changes in the market.
For example, if big data analysis reveals a growing demand for eco-friendly products, a chemical manufacturer can adjust its R&D efforts to focus on developing more sustainable materials. This not only helps in capturing new market opportunities but also strengthens the company’s brand by aligning it with the values of environmentally conscious consumers.
Revolutionize Chemical Manufacturing
Big data is a powerful tool that is revolutionizing chemical manufacturing by enabling companies to optimize operations, predict maintenance needs, and respond more effectively to market demands. By adopting big data technologies, chemical companies can gain a significant competitive edge, allowing them to innovate, reduce costs, and improve product quality in a dynamic and challenging market. As the industry continues to evolve, those who effectively harness big data will be better positioned to thrive and lead in the future of chemical manufacturing.