The chemical industry is on the brink of a profound transformation as it enters the era of Industry 4.0. This new wave of industrial innovation is driven by the integration of advanced technologies such as smart manufacturing, digital twins, and data-driven decision-making. Industry 4.0 is more than just a technological upgrade; it represents a fundamental shift in how chemical companies operate, making them more agile, efficient, and responsive to market demands.
Smart Manufacturing: Revolutionizing Production
Smart manufacturing is at the heart of Industry 4.0, bringing a new level of automation and connectivity to chemical production. By leveraging the Internet of Things (IoT), chemical plants can now connect machines, systems, and sensors in a way that allows for real-time data collection and analysis. This connectivity enables companies to monitor every aspect of the production process, from raw material input to final product output, ensuring optimal performance at every stage.
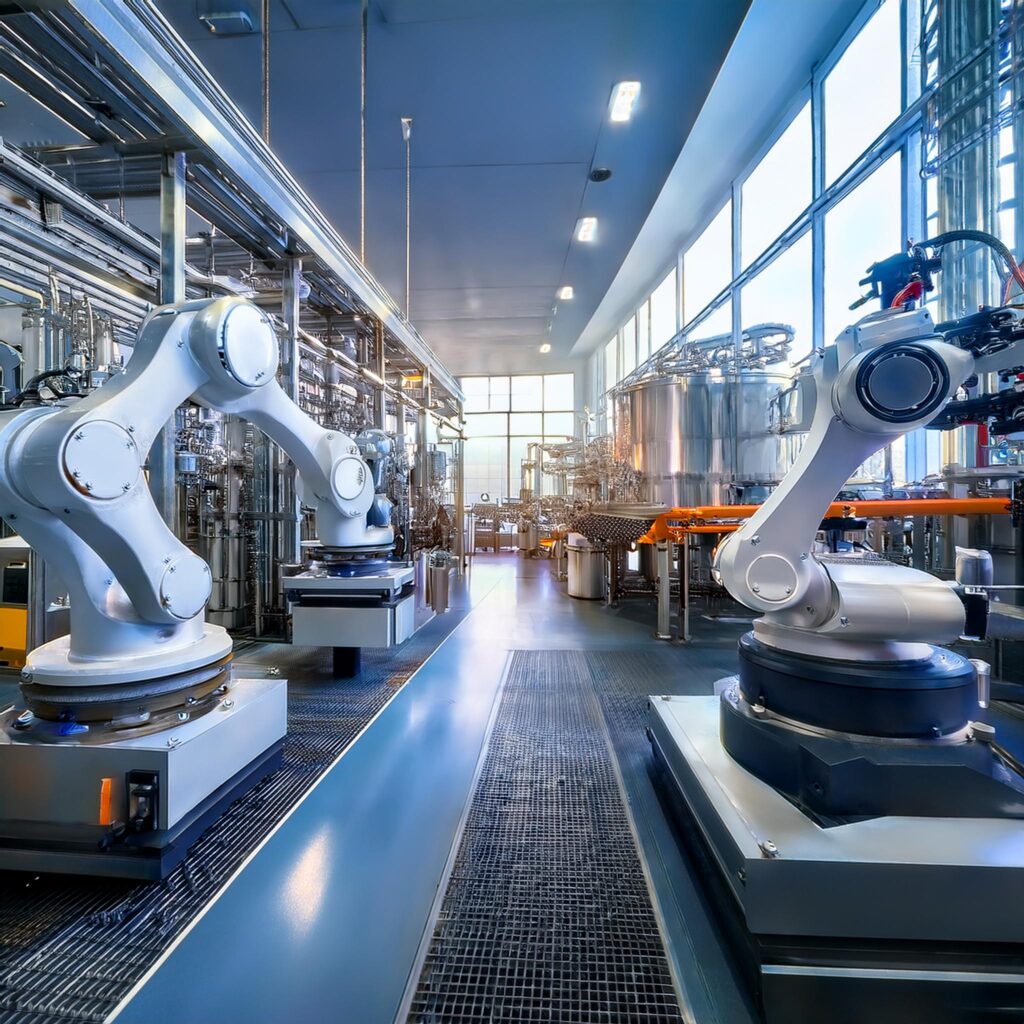
One of the most significant benefits of smart manufacturing is its ability to improve production efficiency. With real-time data at their fingertips, operators can identify and address inefficiencies as they arise, reducing downtime and waste. For example, if a sensor detects a deviation in temperature during a reaction, the system can automatically adjust the parameters to maintain optimal conditions, ensuring consistent product quality.
Moreover, smart manufacturing enables predictive maintenance, where machinery can be monitored continuously for signs of wear and tear. This proactive approach to maintenance reduces the risk of unexpected breakdowns, further improving efficiency and reducing costs.
Digital Twins: Enhancing Process Optimization
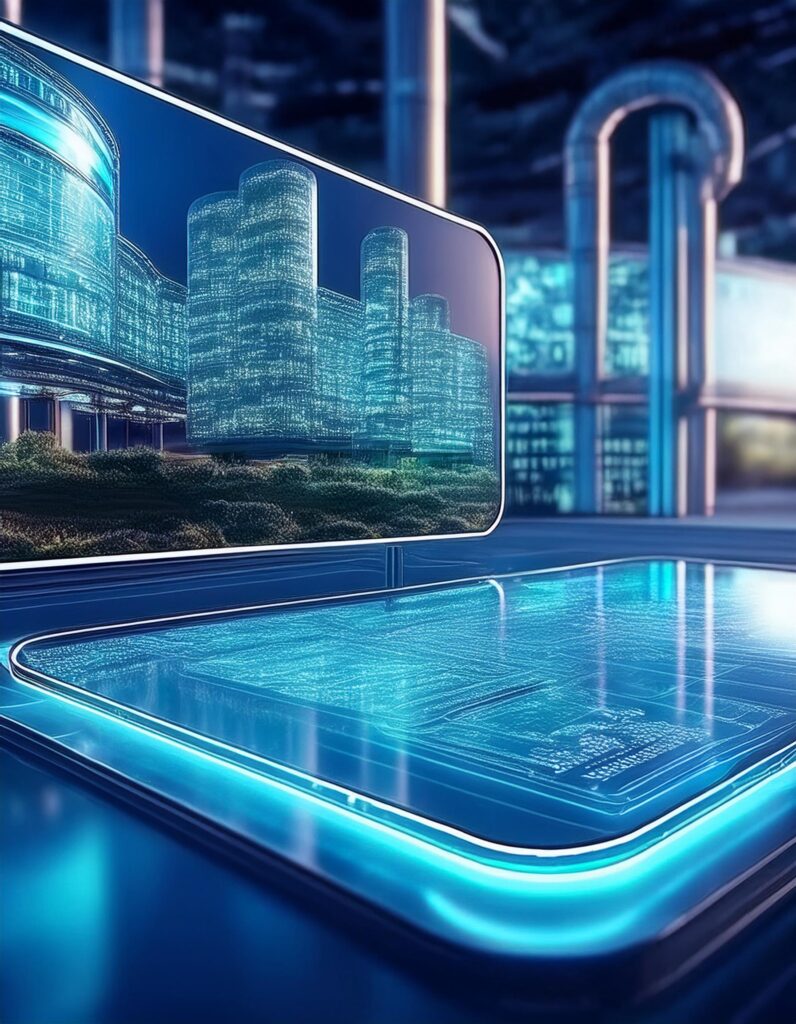
Another key component of Industry 4.0 is the use of digital twins—virtual replicas of physical assets, processes, or systems. In the chemical industry, digital twins are used to simulate and optimize production processes before they are implemented in the real world. By creating a digital twin of a chemical plant, for example, engineers can test different scenarios, optimize parameters, and identify potential issues without interrupting actual production.
Digital twins also play a crucial role in product development. Before launching a new chemical product, companies can use digital twins to simulate how the product will perform under different conditions, allowing them to fine-tune formulations and processes. This not only accelerates the development process but also improves the reliability and quality of the final product.
Gaining a Competitive Edge with Industry 4.0
The adoption of Industry 4.0 technologies is essential for chemical companies that want to remain competitive in today’s fast-paced market. These technologies enable companies to respond more quickly to changes in customer demand, market conditions, and regulatory requirements. By optimizing production, improving quality, and reducing costs, Industry 4.0 provides a significant competitive advantage.
In addition, Industry 4.0 facilitates greater collaboration and innovation within the chemical industry. By integrating digital tools and platforms, companies can work more closely with suppliers, customers, and partners, sharing data and insights to drive innovation across the value chain.
As the chemical industry continues to evolve, those who embrace Industry 4.0 will be best positioned to lead the next industrial revolution. By leveraging advanced technologies to enhance every aspect of their operations, these companies will not only survive but thrive in the face of increasing global competition.